Anybody out there ever bend their own lexan before? I'm going to give it a shot. I've read a bit on line about how to and it sounds like I can either heat the lexan in the oven, or using a propane torch carefully, heat the area I want to bend while it's over a pipe (for the radius I need)...
Any tips or special tricks I should know about before I do this from someone who has tried before?
Remember, I'll be working with Lexan, NOT plexiglass!!!
I'm moving my electronics INTO my center console instead of on top of it. The existing lexan "door" is hinged in the center (horizontally) and I want one single piece so I can see through it.
I just didn't like how wet the Furuno and Raymarine got last Friday and Saturday, so I'm moving them "under cover"!!!
Thanks!
Bending Lexan...
Moderators: bman, Chalk, Tom Keels
Re: Bending Lexan...
http://www.hotrodders.com/forum/how-ben ... 26467.html
.. the heating blanket suggestion in the above link looks good to me.
.. the heating blanket suggestion in the above link looks good to me.
use your opportunities ...
218 Carolina Skiff
25 Bayliner Deck
218 Carolina Skiff
25 Bayliner Deck
Re: Bending Lexan...
Dukes, oddly enough I actually spent some time between high school and college as a professional bender (yes like the robot on Futurama). I worked almost exclusively with Lucite and Lexan. Tips - it's all about the exact right temperature, which we used to eyeball because from one batch to another of the raw Lexan sheets they would have slightly different tolerances. If you bend it too cool you will get cracks in the bend, which are usually blatantly obvious when it happens. If you let it get too warm, it will melt and boil. when that happens, you get bubbles in the heated portion(s) and of course there's no undoing that.
Tricks - here's how we did it at the factory - We used a long 2x4 laid down flat on a table with a channel cut right down the center. we had other 2x4's on either side we could move back and forth to support the rest of the sheet or piece. Inside that channel we had a piece of what I guess you would call medium gauge non-insulated copper wire. That wire came off each end of the 2x4 and was plugged in to a VARIAC rheostat dealie. Really simple circuit. So we turn on the VARIAC to a relatively low setting and let the wire heat up to an ambient, then could make small adjustments as needed. Then we lay the sheet or piece to be bent on top of that 2x4 - that whole channel effectively becomes fairly even convection heat. When it gets warm enough to bend it will begin to look a little warped like a really old glass window on an antique house. Not far past that you get bubbles. When it starts to blur a little along the heat source, very gently 'feel it out' and see how willing it is to bend. If it's warm enough, it will bend without much pressure on it. Ideally, you want to bend it as cool as possible without breaking it, because it will cure / dry / set faster with less elasticity (basically you don't have to hold it in place as long to cool).
Now for cooling our bends, we actually used 1/8" or 1/4" thick sheets of Lucite laser-cut to exact angles/shapes/sizes, but basically, what we had was like a flat sheet with channels cut in it to fit the piece we are bending. when the temperature was correct, we pull it off the heat source and insert it in the channels cut out of the flat 'cooling sheet' - this in my experience is the ONLY way to get it to cure at the exact intended angle; a human just can't do it right in my experience because it takes forever to cool and has a lot of 'memory' as to wanting to bend back flat. even when it feels rock solid to the touch, if it's still warm, it will move after you give up and leave the room. For 1/16th inch sheets we used to leave the bends in these little cooling sheets for 1.5-3 hours. You could do this to slightly less exacting standards with a thin sheet of plywood and a jigsaw I reckon for a shade-tree substitute.
Again, it's all about the temperature, and too low is way better than too high. If you leave it on low heat long enough it will eventually reach its bending/melting point without boiling. I can't tell you how many sheets I boiled and ruint forever getting impatient and turning up the heat instead of waiting. Bend, don't break, and certainly don't boil.
Did I lose you yet? I'd draw you some pictures if I wasn't so lazy, but if you have any questions feel free to hit me up. I also used to butcher gators. I had a lot of weird jobs.
Tricks - here's how we did it at the factory - We used a long 2x4 laid down flat on a table with a channel cut right down the center. we had other 2x4's on either side we could move back and forth to support the rest of the sheet or piece. Inside that channel we had a piece of what I guess you would call medium gauge non-insulated copper wire. That wire came off each end of the 2x4 and was plugged in to a VARIAC rheostat dealie. Really simple circuit. So we turn on the VARIAC to a relatively low setting and let the wire heat up to an ambient, then could make small adjustments as needed. Then we lay the sheet or piece to be bent on top of that 2x4 - that whole channel effectively becomes fairly even convection heat. When it gets warm enough to bend it will begin to look a little warped like a really old glass window on an antique house. Not far past that you get bubbles. When it starts to blur a little along the heat source, very gently 'feel it out' and see how willing it is to bend. If it's warm enough, it will bend without much pressure on it. Ideally, you want to bend it as cool as possible without breaking it, because it will cure / dry / set faster with less elasticity (basically you don't have to hold it in place as long to cool).
Now for cooling our bends, we actually used 1/8" or 1/4" thick sheets of Lucite laser-cut to exact angles/shapes/sizes, but basically, what we had was like a flat sheet with channels cut in it to fit the piece we are bending. when the temperature was correct, we pull it off the heat source and insert it in the channels cut out of the flat 'cooling sheet' - this in my experience is the ONLY way to get it to cure at the exact intended angle; a human just can't do it right in my experience because it takes forever to cool and has a lot of 'memory' as to wanting to bend back flat. even when it feels rock solid to the touch, if it's still warm, it will move after you give up and leave the room. For 1/16th inch sheets we used to leave the bends in these little cooling sheets for 1.5-3 hours. You could do this to slightly less exacting standards with a thin sheet of plywood and a jigsaw I reckon for a shade-tree substitute.
Again, it's all about the temperature, and too low is way better than too high. If you leave it on low heat long enough it will eventually reach its bending/melting point without boiling. I can't tell you how many sheets I boiled and ruint forever getting impatient and turning up the heat instead of waiting. Bend, don't break, and certainly don't boil.
Did I lose you yet? I'd draw you some pictures if I wasn't so lazy, but if you have any questions feel free to hit me up. I also used to butcher gators. I had a lot of weird jobs.
Mookbait! At least 401 times better than live bait!
He who have signature line make bigger post.
He who have signature line make bigger post.
Re: Bending Lexan...
Mook: You didn't lose me and everything you offer is really appreciated.
I had a piece in the garage (1/2" thick). Put it flat on some plywood and put the torch to it. I found out what impatience will get me (white/burned lexan), but I also found what patience will get me... A perfect bend. A cooling jig is in order, because I did find out how long it takes it to actually cool off without reverting itself to it's original shape! Wow, that stuff has better memory than me! I do know what you mean about the look of antique glass though. As soon as I saw gravity bending it, I shut off the torch and gently pressed down to make my bend.
You see, all I've got to do is bend a 90 degree angle in mine.
I've got 2 more "practice pieces" to play with before I work on the real thing, so I'm feeling pretty confident, but not TOO confident.
Awesome help though!!!! Thanks!
I had a piece in the garage (1/2" thick). Put it flat on some plywood and put the torch to it. I found out what impatience will get me (white/burned lexan), but I also found what patience will get me... A perfect bend. A cooling jig is in order, because I did find out how long it takes it to actually cool off without reverting itself to it's original shape! Wow, that stuff has better memory than me! I do know what you mean about the look of antique glass though. As soon as I saw gravity bending it, I shut off the torch and gently pressed down to make my bend.
You see, all I've got to do is bend a 90 degree angle in mine.
I've got 2 more "practice pieces" to play with before I work on the real thing, so I'm feeling pretty confident, but not TOO confident.
Awesome help though!!!! Thanks!
Re: Bending Lexan...
1/2" is pretty tough to get right. I'd think with a torch you're going to get excessively uneven heat on the top vs bottom vs inside of a 1/2 inch cut (kind of like cooking a thick steak on high heat). Lexan doesn't transfer heat well; that's why it takes so long to cool, so unless you got some sort of space-aged low temp torch (I ain't a torch expert) you're going to get a much lower quality bend, more blurriness, less precision. If it's turning black then it sounds like you're scorching / searing it with the torch. If you're getting a white line or stripe in the crease that means it bent at too low a temperature.
Just thought of something that might work really well for you to get the heat more even if you have or can find the materials; just a larger scale shade tree version of what I used to use - get a sawhorse with metal frame and find a small metal pipe made of a metal that conducts heat really well and cut it a little longer than your bend. Place pipe between the planks on the sawhorse and heat the pipe with the torch until it gets nice and warm, then after it's pretty hot set your sheet on the sawhorse over it (add a couple wood blocks or something as shims if you need to raise it slightly to get clearance over the pipe). Like I said, cut or find pipe a little bigger than the length of the sheet you're bending and you can continue to heat the pipe with the torch on each protruding end.
Sounds like you're doing well all things considered, but one big tip I would offer is that if you're letting gravity start the bend, that will usually happen when it's just below prime bending temperature, which could very likely result in the white crease even in an otherwise perfect job. That's why I recommend rigging some version of the 'channel' heating I explained before. That way you're placing the Lexan sheet flat over the heat source, and it should be supported as close as possible to each side of the heat source to keep it from bowing down in the middle once it warms up as that will also cause the white crease line.
Just thought of something that might work really well for you to get the heat more even if you have or can find the materials; just a larger scale shade tree version of what I used to use - get a sawhorse with metal frame and find a small metal pipe made of a metal that conducts heat really well and cut it a little longer than your bend. Place pipe between the planks on the sawhorse and heat the pipe with the torch until it gets nice and warm, then after it's pretty hot set your sheet on the sawhorse over it (add a couple wood blocks or something as shims if you need to raise it slightly to get clearance over the pipe). Like I said, cut or find pipe a little bigger than the length of the sheet you're bending and you can continue to heat the pipe with the torch on each protruding end.
Sounds like you're doing well all things considered, but one big tip I would offer is that if you're letting gravity start the bend, that will usually happen when it's just below prime bending temperature, which could very likely result in the white crease even in an otherwise perfect job. That's why I recommend rigging some version of the 'channel' heating I explained before. That way you're placing the Lexan sheet flat over the heat source, and it should be supported as close as possible to each side of the heat source to keep it from bowing down in the middle once it warms up as that will also cause the white crease line.
Mookbait! At least 401 times better than live bait!
He who have signature line make bigger post.
He who have signature line make bigger post.
-
- Site Sponsor
- Posts: 12120
- Joined: December 12th, 2001, 8:00 pm
- Location: Tallahassee
Re: Bending Lexan...
DukesFin - I forgot to mention, there is really no such thing as a 90 degree angled bend with most of those synthetic super-plastics. Their molecular bond is sort of like crystalline made of elastic - you can stretch each bond a little bit without breaking / smashing it. Smashing the bonds is what causes the white lines you get from bending too cool. As such, they can only really be bent in a 90 degree arc. If you need an actual 90 degree flat angle like the letter "L" then the 'right' way to do it is cut it in half, cut screw holes and use some special friction screws to fasten them together flush at 90deg. I don't know any way to get the precise cuts and screw holes for that without a giant "laser."
On your cooling template for a 90 degree arc, you want to cut out two channels that are perpindicular bisectors of a circle. The diameter of the circle will dictate your arc length. As long as the circle doesn't get too big or too small, the natural memory of the material will lend itself to making a perfectly graded symmetric arc (another reason slow even heating is emphasized - uneven heating will distort this tendency). Also if you're bending 1/2" Lexan, you need to cut the two straight channels only a small fraction of an inch wider than your material, maybe 17/32" total width so there isn't room for any play in there, which would also distort the angle of your bend for obvious reasons.
I got slightly less lazy and drew you a half-arse picture of what we'd cut in a board to shove it in after you heat it.
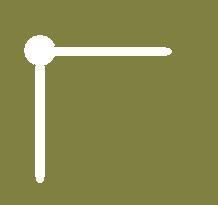
Another thing that would probably work in lieu of wasting 4 hours of precision jigsawing is take a piece of plywood or something that's perfectly squared, then lop off one corner (make sure it's a 45/45/90 triangle you cut off) so you're cutting off 3/4" to 1" or so off each side. wrap your heated sheet around the edges without forcing the bend. Once you get it wrapped up, you could shove it in the corner of a room if you have one with no molding or baseboards so that the walls keep it from bending the other way. Put something heavy on the board so it don't move away from the wall - presto. As far as I know there's no need for an actual circle like I drew there; we just cut ours that way because it was easier in the CAD programs if you started with a circle.
Anyhow, if I write any more on this topic I'm going to need an editor and publisher, maybe a team of attorneys, but just wanted to explain that all to you because it you're going for a flat 90 angle instead of arc, you're not ever going to get it perfect with a heated bend because of the protons and the electrons and stuff and it's thus crucial that your cooling jack facilitate a well formed arc.
On your cooling template for a 90 degree arc, you want to cut out two channels that are perpindicular bisectors of a circle. The diameter of the circle will dictate your arc length. As long as the circle doesn't get too big or too small, the natural memory of the material will lend itself to making a perfectly graded symmetric arc (another reason slow even heating is emphasized - uneven heating will distort this tendency). Also if you're bending 1/2" Lexan, you need to cut the two straight channels only a small fraction of an inch wider than your material, maybe 17/32" total width so there isn't room for any play in there, which would also distort the angle of your bend for obvious reasons.
I got slightly less lazy and drew you a half-arse picture of what we'd cut in a board to shove it in after you heat it.
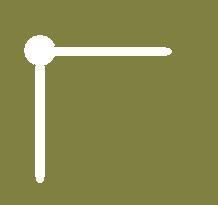
Another thing that would probably work in lieu of wasting 4 hours of precision jigsawing is take a piece of plywood or something that's perfectly squared, then lop off one corner (make sure it's a 45/45/90 triangle you cut off) so you're cutting off 3/4" to 1" or so off each side. wrap your heated sheet around the edges without forcing the bend. Once you get it wrapped up, you could shove it in the corner of a room if you have one with no molding or baseboards so that the walls keep it from bending the other way. Put something heavy on the board so it don't move away from the wall - presto. As far as I know there's no need for an actual circle like I drew there; we just cut ours that way because it was easier in the CAD programs if you started with a circle.
Anyhow, if I write any more on this topic I'm going to need an editor and publisher, maybe a team of attorneys, but just wanted to explain that all to you because it you're going for a flat 90 angle instead of arc, you're not ever going to get it perfect with a heated bend because of the protons and the electrons and stuff and it's thus crucial that your cooling jack facilitate a well formed arc.
No sir...BUTCHER. The skinner did the gutting by default. Skins are worth more than the rest put together, so salty old Cajun dudes with tons of experience were the only ones allowed to skin em.Jumptrout51 wrote:Gator Gutter?
Mookbait! At least 401 times better than live bait!
He who have signature line make bigger post.
He who have signature line make bigger post.